It is common for Maintenance Supervisors to be faced with the challenge of certifying their maintenance welders.
The most common reasons this comes up are…
- The need to avoid liability while making weld repairs on life-critical equipment, machinery, or structures where failure could result in death. (Examples include: cranes, tie-off points, boilers, high pressure piping, bridges, and structural building members.)
- The need to make weld repairs on equipment or machinery without voiding the warranty.
- The need to determine who has the most skill for promotion or hiring purposes.
No matter the cause, every Maintenance Supervisor should be aware of the following three myths before they certify their welders.
Myth #1: My company won’t be liable if a certified welder makes our welds.
Most companies assume that if they have a certified welder making welds, they are protected from liability and can weld anything they want. While it is true that any weld that is made should be made by a certified welder, that is only part of the equation.
For a company to be protected against liability, the weld has to meet three criteria. It has to…
- Be made by a certified welder;
- Follow a qualified procedure; and
- Pass the appropriate inspections.
These three things must support any weld in order to reduce liability. Remove any one of these three, and the company is exposed to liability.
Certifying welders is just one step in the process of making good welds. Once the welders are certified, appropriate WPSs have to be qualified and maintained for every weld that is made. After a weld is made, it has to be inspected in accordance with the appropriate code or standard.
Welding Audits LLC is able to help with all the steps in this process. Let us help you reduce liability by creating and maintaining the appropriate documents and procedures.
Myth #2: One qualification covers everything
There is no one weld test that qualifies a welder to do everything.
In order to make a warranty-qualified weld on a specific piece of machinery, the welder has to…
- Be qualified to the appropriate standard;
- Make the weld by following a WPS (Welding Procedure Specification) designed for that specific machinery; and
- The weld must pass the appropriate inspections.
Each one of these variables can change from one situation to the next. This means that a welder who is qualified to do a weld repair on one piece of equipment may not be qualified to make repairs on a different piece of equipment.
The most widely used welding code in the United States is the AWS D1.1 Structural Steel Welding Code. The D1.1 code states that changes in certain variables beyond those qualified, requires requalification of the welder. (See Figure 1)
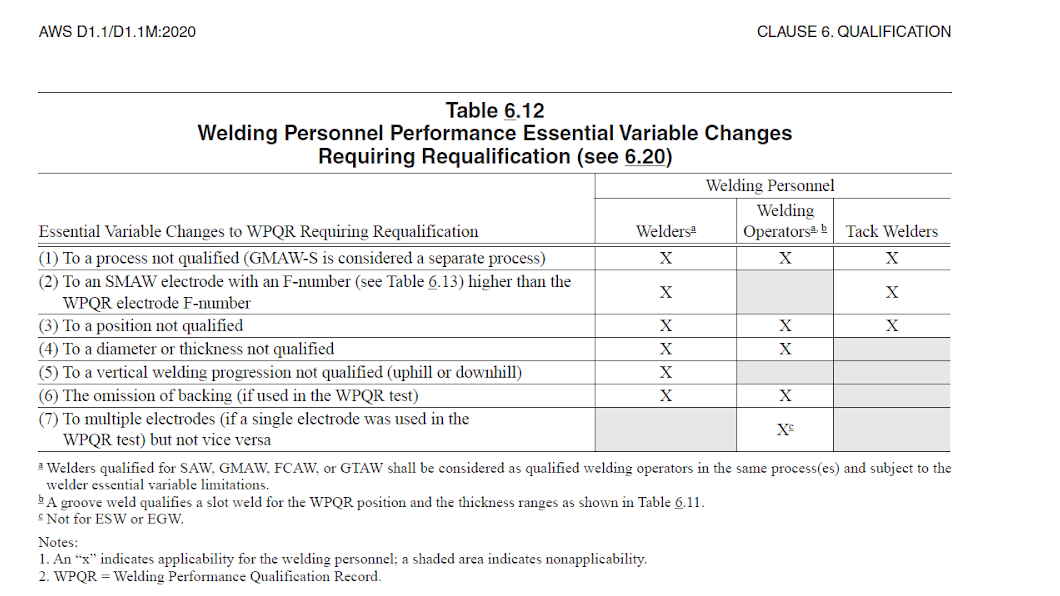
Figure 1
All welds rest on three things
- Qualified Welders
- Qualified Documents
- Appropriate Inspections
Even if it were possible to give a welder a combination of weld tests that qualify them to weld “Everything,” that certification would only be good for as long as the welder continued to demonstrate the ability to make the weld.
Myth #3: Once certified, always certified
The D1.1 code (see Figure 2) says that welder certification is good indefinitely…
- Or for 6 months after the last time the welder used the process,
- Or until there is reason to question the welder’s ability.

Figure 2
Just because a welder was certified twenty years ago, or even last year, does not mean that certification is valid today.
Failure to consistently meet the minimum inspection requirements on every weld is a valid reason to question a welder’s ability and require requalification. It does not matter how good a welder used to be, only how good they are today. Every welder is only as good as the next weld they can make.
It is common for welders who have been certified to the minimum standard allowed by the code to regularly produce welds that are not acceptable. It is an issue of “aim small, miss small”. Those who practice welds that far exceed the code minimum are more likely to consistently pass the code minimum then those who practice only to the code minimum.
Summary:
Don’t let improper welds expose you to costly liability or voided warranties . If you are trying to get your maintenance welders certified and want to make sure it is done right, then contact Welding Audits LLC. We take all the frustration and confusion out of ensuring that all three legs of your weld quality system are stable and working properly.